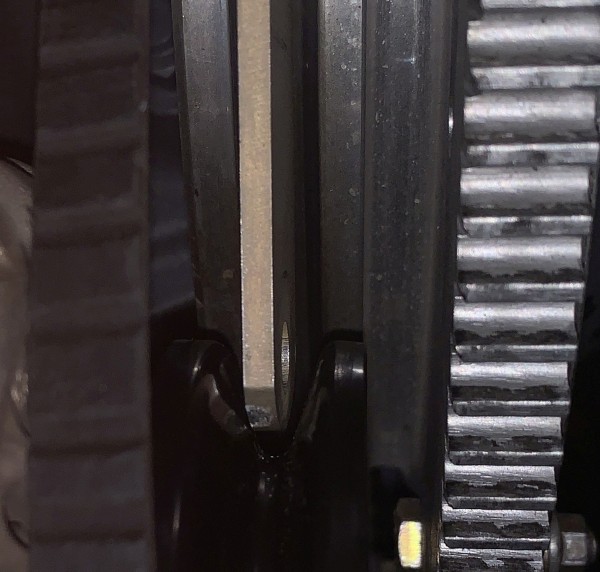
|
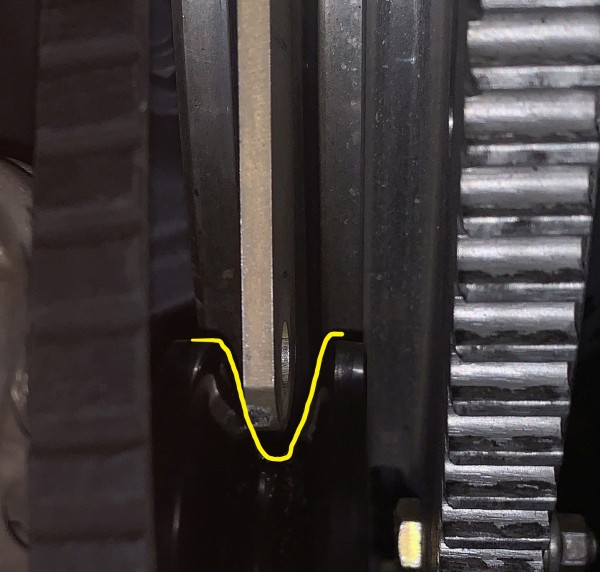 |
The pictures above and below show that if you slide the
alternator adjuster bracket along the big pulley on the
engine, and lift the alternator, you can use it as a guide
to show where the groove will line up by seeing where the
bracket hits the alternator pulley. It is very hard
to get good pictures at the perfect angles because you
have to make sure to align the camera lens with the
pulleys to get the best view, but even though these aren't
perfect, I've duplicated the picture and drawn in the
pulley edge in yellow so you can see the misalignment
better.
Notice that the bracket hits the left side of the pulley
about 1/4-1/3 of the way up from the bottom of the groove,
rather than being centered.
It was very hard to get an approximate measurement but I'm
guessing something around .093"-.095" of a shift was what
was required to center it. The 403-301-4 I think
moves it .130" which makes the adjustment bar dig into the
other pulley face.
|
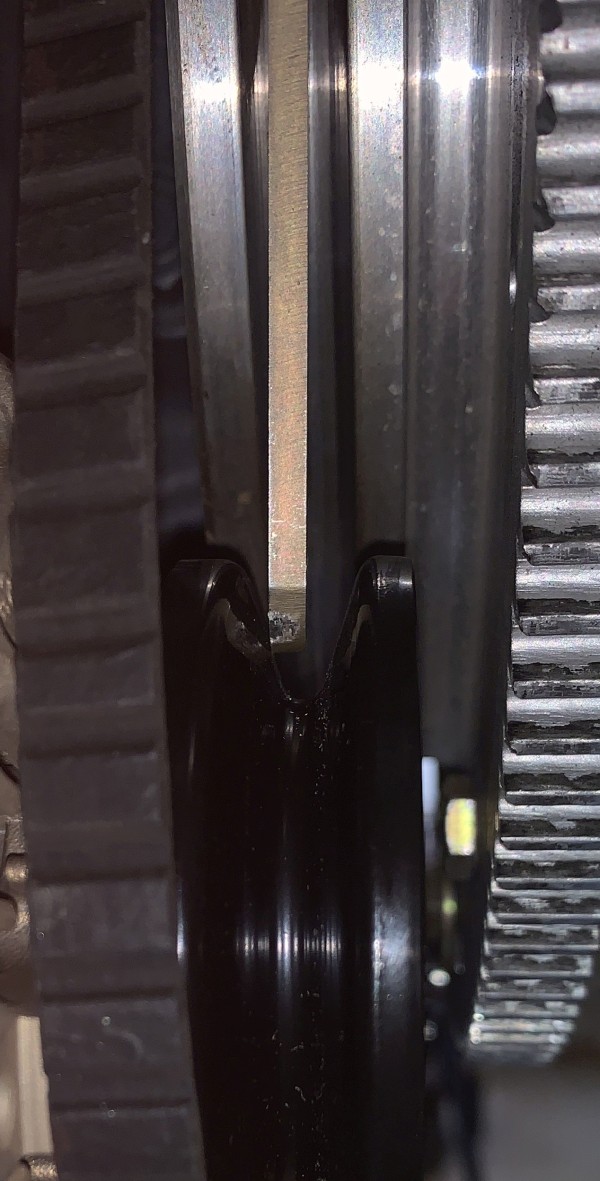
|
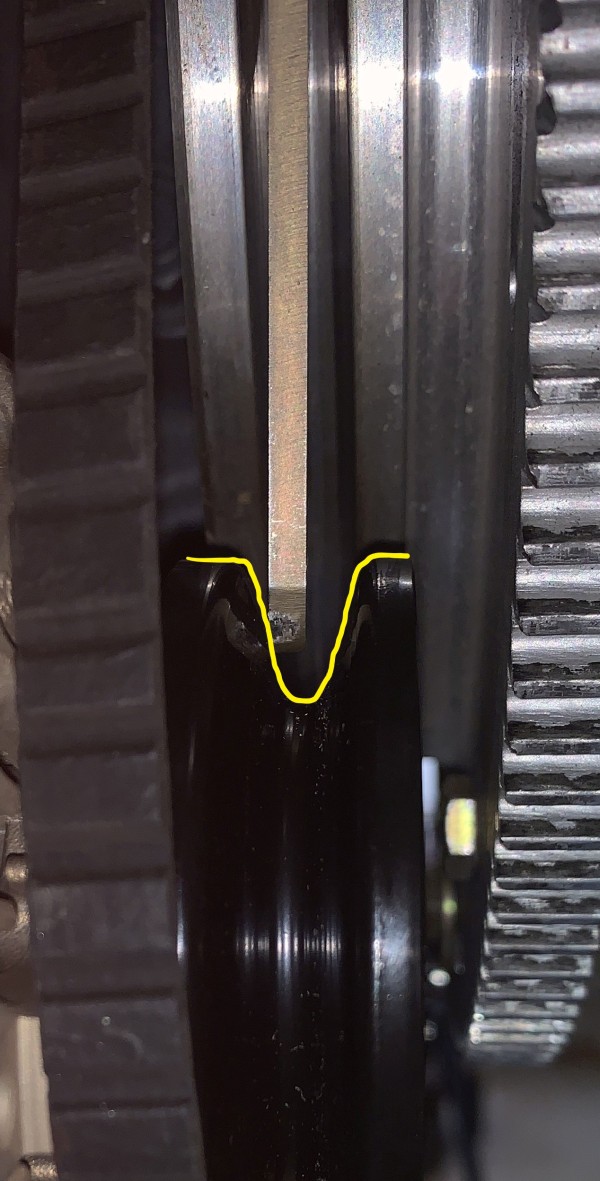
|
|
|
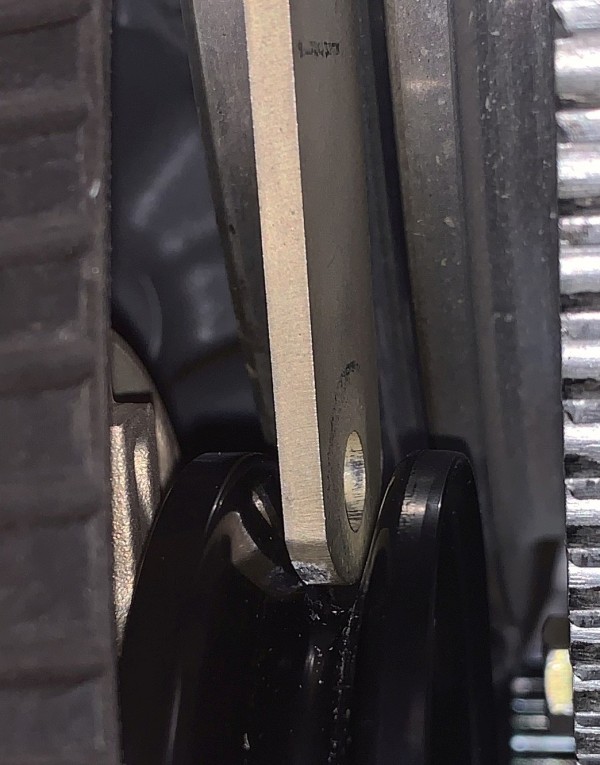 |
This is just another view
so you can see the edge of the bracket digging into the
pulley.
|
|
|
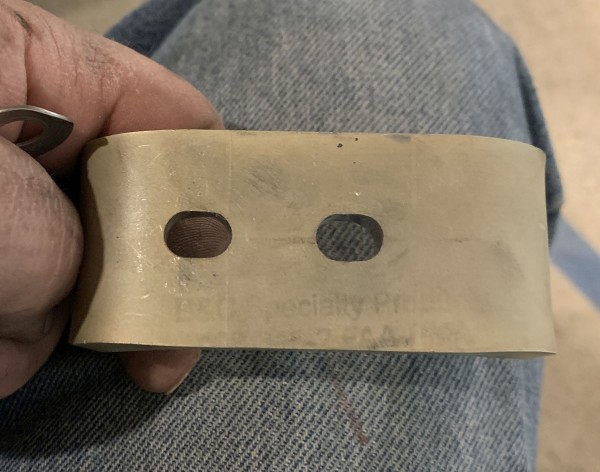 |
This is the oblonging of
the holes that I had to do, to get the alignment
proper. I had to elongate not only the round hole,
but the oval one as well. The engine bolts, by
default, center up in the middle of the oblong hole on the
original bracket, when both bolts are in. The extra
space in the oblong hole is not enough after making the
round hole also oblong, to fix the misalignment, so both
had to be filed.
|
|
|
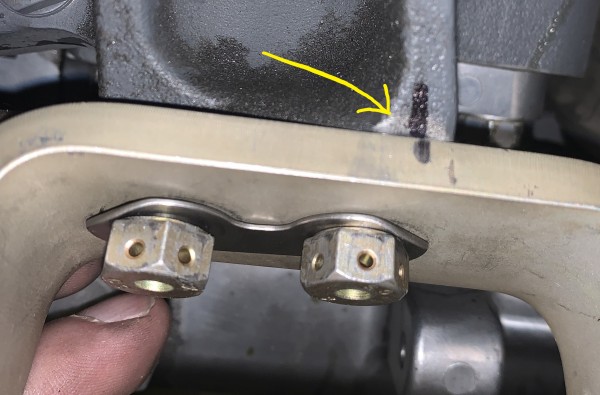 |
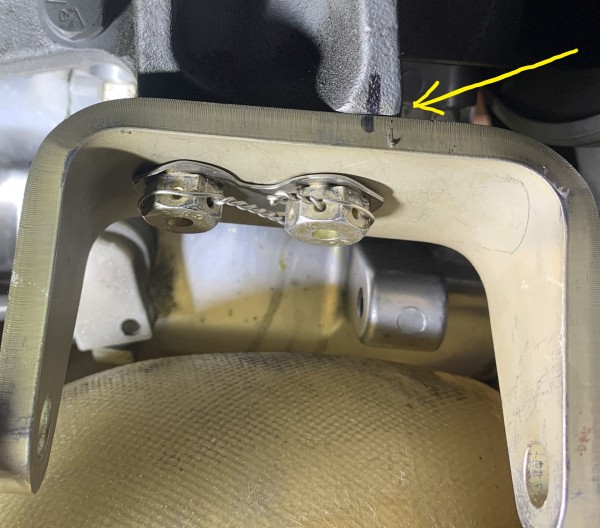
|
These 2 pictures above are a poor attempt to show the
amount of shift. I originally filed the holes a
little too far, so the bracket could be slid too far in
the necessary direction, so I needed to make a mark so
that I could have a reference when torquing up the bolts
to know that I was moving it the right amount. In
that process, I tried to take a couple of pictures of the
mark so I could show how much the bracket needs to be
moved. But, since there are no references such as
the thickness of the marker line, it's not really useful
for precision measurement, only for illustrating
approximate shift necessary to align.
|
The following 3 pictures show the adjuster arm in position
after correcting the misalignment. You can see that
the arm fits nicely into the base of the V groove as well
as can be expected.
|
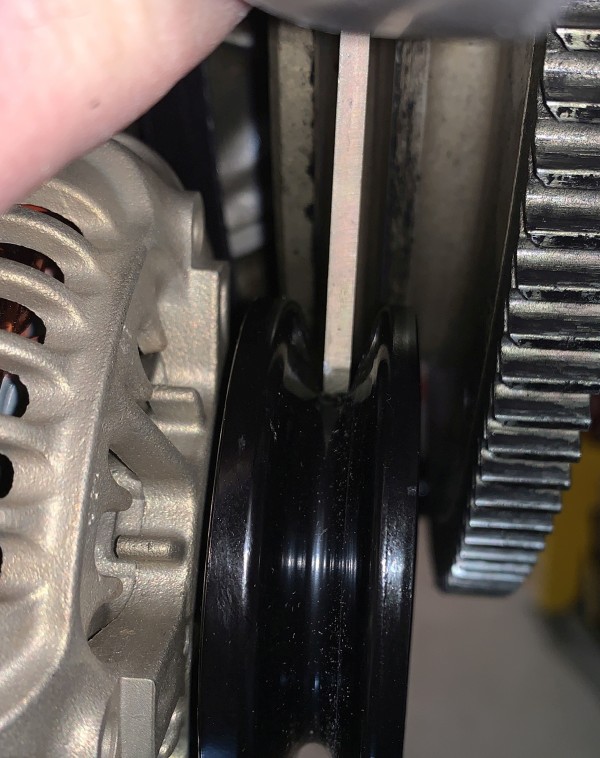 |
|
|
|
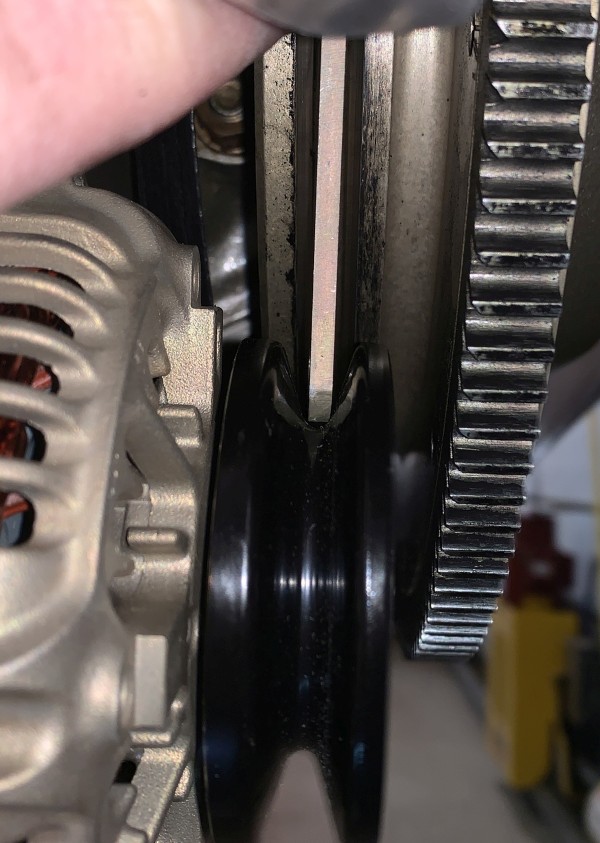 |
|
|
|
 |
|
One additional issue that I encountered is that the
adjuster bracket should either be bent, such as
Plane-Power does with their brackets (which are much
thicker), or a second thick washer should be
included. The gap between the adjustment arm and the
alternator on both of my planes, IO-540 Narrow Deck and
IO-390 Wide Deck, was about double the thickness of the
thick washer that you supply with the alternator. I
had to find washers with the same OD and drill them out
for the same size center hole. Since I didn't have
thick washers, I had to use 2 standard washers in additon
to the thick one supplied with the alternator. This
shows the gap and the stack.
|
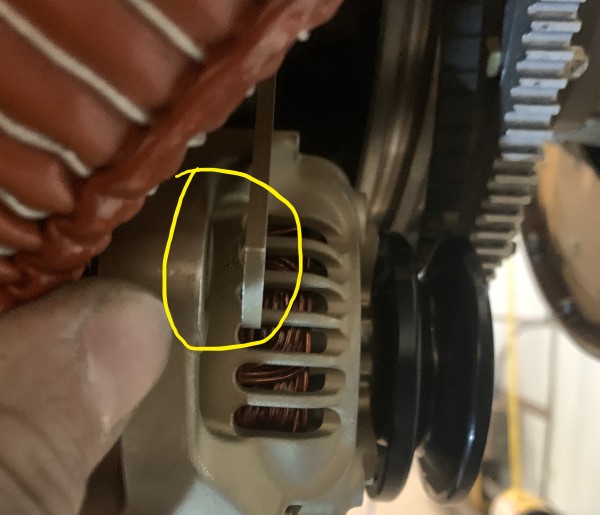 |
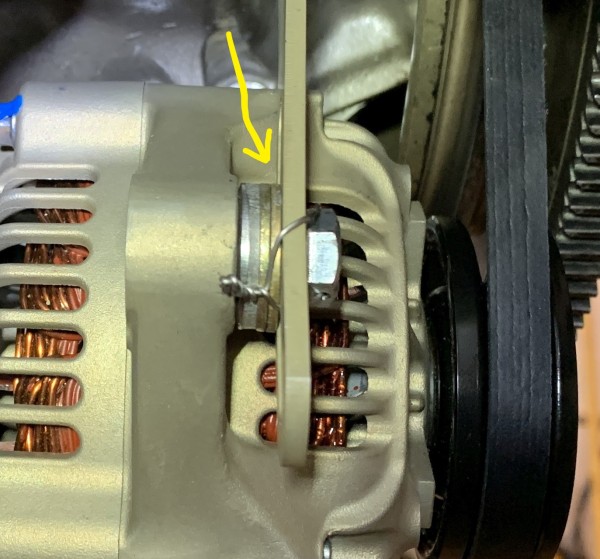 |
|
|