New Safety-Trim Trim Servo Controller
Added 10/27/07 - 286 hours
Updated 2/28/09
Why worry about the trim system?
Ever since I was just a few hours into my flyoff of my RV-10,
almost two years ago now, I've had one nagging issue with the RV-10.
For those of you who've joined me for a demo flight, you probably even
got this pointed out to you. The elevator in the RV-10 has a LOT of
authority, and so does the elevator trim system. During my flyoff
period, I was going through a manual in a binder, and it laid on the
top of the stick while I was reading it. I was hands-off on the
airplane, and suddenly the airplane was climbing like a rocket!
From that moment on, I had a lot of respect for what could happen with
an inadvertent trim activation. I decided that SOME DAY, I would have
to find a good fix for that problem. One that worked well and was well
thought out and addressed the trim speed issue during cruise.
Ever since I started giving demo flights, I give a couple of standard
statements: "Go ahead and fly the plane as you would your
own. Don't be afraid to do steep turns or whatever you are
comfortable with. But, be aware that while the roll forces get
very stiff at higher speeds, the pitch forces are very light, so be
easy on the elevator. And, the trim works very quickly...here,
let me show you....now that we're flying level, hold the trim switch
back for a count of 1 second..." That's usually the point where
their eyes bug out when they see how much trim you can get at
full-speed in 1 second. I've made it a point to show people going
all the way back, so obviously I believe that it's an issue. I just
didn't have the luck of finding the right off-the-shelf system to fix
it until now.
One thing that I strongly suggest for most people, and ALL people with
kids, is the addition of a Co-Pilot trim disconnect switch. On my
panel, I have a lever-locking switch that basically just cuts off the
ground lead to the trim switches on the co-pilots stick. (Note: I used a NKK Lever-locking
ON-OFF-(ON) switch that is pretty cool, mouser.com
has them p/n 633-M2019LL1G01)
As many of you
know, the trim relays are activated by switching a wire to ground, and
so by switching off the ground on the co-pilot stick that feeds all of
those circuits, you can easily and effectively disable their trim
switches. I had that feature installed since day 1, and it is VERY nice
when hauling the kids around the sky...not to mention those inquisitive
buddies of yours who like to push buttons about 3 seconds before they
ask what the button does.
Fast forward a year and a half to OSH 2007. On my way to OSH to
grab my campsite, I had my first instance of a sticky trim relay. The
old style Ray Allen relays are seemingly prone to sticking, and they
now use a different relay that is larger to prevent the problem.
I had the trim stick about 4 or 5 times in the days surrounding OSH,
and on at least one landing I was forced to land the plane holding a
lot of stick force. Read
my report here about changing out those relays. After changing them
out, all was well again, although discussions on the Matronics RV-10
list got me thinking. There are those who wonder, why do we use old
mechanical relays for trim activation when these days there are great
and reliable ways to do it via solid-state? There is a certain comfort
level of using relays, because they don't use "magic" like transistors,
but if you've ever watched the track record for mechanical limit
switches and relays you'd probably find that there's a reason
"solid-state" became a popular phrase many years ago.
Address Trim Cautiously!
One of the biggest reasons that it took me 285+ flying hours to address
the trim speed issue is the fact that playing around with your trim is
serious business. I don't know how to get that point across better than
to take you out, let you fly, and activate the trim for 1
second....just ONE second, in cruise, and then disable your stick trim.
You would be AMAZED at how hard to manage the aircraft will become.
This means that if you install an aftermarket (or for that matter, the
Van's standard) trim system, you want it to be reliable and safe. I've
had the opportunity to look at a few different trim systems, and you
have to pay close attention to the details. One system used
Pulse-width-modulation to pulse the DC power to the motor, so you could
maintain the source at 12V, which keeps the motor from lagging. This in
itself was cause for a small bit of concern, because AC or pulsing DC
circuits can be a cause of noise in your electrical system. That
particular system used a microprocessor to keep the trim at 1/2 speed
for 1/2 second, then begin ramping it up over the 2nd one-half second,
and at that point it would run at full speed. 3 problems there...one is
that microprocessors run code, and can become flaky or erratic after an
electrical surge or spike. Not good. I'm not ready to trust a
microprocessor circuit driving my control surfaces like that. Sure, and
Autopliot does it, but autopilots are designed to be able to be easily
overridden by the pilot. Trim systems are NOT. The second problem with
that system is that if you accidently laid a book on the trim switch
like I did, you'll get a gradual application of trim, but very shortly
thereafter it'll be full speed, and you'll get out of whack really
quick. The 3rd problem is that when you're in the pattern, you're
not going to get any full-speed trim operation until you've waited 1
full second of holding the switch. The RV-10's standard trim motor is
fast enough at low speed to be great, but if you induce a lag into it,
you might not like how quickly the trim reacts during takeoff and
landing.
Enter the Safety-Trim system...
The Safety Trim System
Note: I have
no interest in any company mentioned on this page
and I wrote the write-up and informed the RV-10 community before I even
informed Bob that I had completed and tested the installation.
Bob's
an RV-10 builder who designed this trim system based on feedback he
received previously on the RV10-List and from comments that I provided
regarding RV-10 flight qualities as he was near the end of product
refinement before he released it for sale.
Coincidentally, just as I was planning to address the trim speed during
cruise issue within the next month or two, I ran into Bob Newman, of
TCWTech.com, maker of a new trim system called the "Safety-Trim"
system. I spoke with him on the phone and at the time he had just
been getting ready to release the system for sale. It was a case
of perfect timing. As we talked, I was initially skeptical, as I
usually am with any small-product offering from a small business, but I
quickly became interested when we discussed trim system theory.
Bob used a voltage controlled system for reduction in trim speed, due
to the noise possibilities of PWM mentioned above. He also is a
believer in being able to recover from a stuck or broken trim switch
(something I'm a little less concerned with) by reversing the trim
system. He appreciates having a panel mounted switch that can be
used for both disabling the trim in an emergency, or reversing it,
should the need arise. The thing that really stands out though is
that he wanted a system that would PREVENT a crash from being caused by
a runaway trim in the first place, and he had a way to do that.
Let me show you how...
Bob designed a method into his trim controller that would limit servo
operation to 3 seconds per switch activation. Should you release
the switch for just a few milliseconds, you get another 3 seconds of
trim. Using this method, he can prevent the trim system from
running all the way to a limit...or even from running far enough to
make the plane uncontrollable. But, wouldn't this use a
microprocessor that I then couldn't trust? Nope, his trim system
is driven by an analog circuit that is designed to just plain stop
working if a component blows out. No runaway trim operation here.
Additionally, his trim system provides 2-axis control, so you can use
one circuit for elevator, and the other for either aileron or
rudder. (Note: If you are installing rudder trim, and I do
suggest that, then I'd use Elevator + Rudder with this
controller) It is short-circuit proof, and protected from reverse
polarity, and is compatible with the common Ray Allen trim servos and
switches.
How the panel mounted switch works is really kind of nice too. He
uses an ON-OFF-(ON) switch for the trim system. If you turn it
ON, the trim system will work. Most people will just leave the
switch in that position all the time. Should you ever experience
a trim system problem, you have the option to turn the switch to the
OFF position in the middle. The (ON) position is a momentary
position that runs the reversing function. You must HOLD the
switch with one hand and run your trim with the other hand to utilize
this function...a good thing, too, because inadvertently reversing your
trim could be a big problem. One side note here: I *really* don't
think a person needs more than the switch that Bob provides with the
system...however...I already utilitize a lever-locking switch for my
co-pilot trim disconnect, and I decided that just to ensure that nobody
would ever bump my trim switch to the OFF position, I added a NKk
M2019LL1G01 Mini Lever-locking ON-OFF-(ON) switch to my panel in place
of the one he sent. (Update: I have had 2 times where even with a
lever-locking switch I have managed to bump the system off while
playing around with things pre-flight, so I now am even more solidy of
the opinion that lever-locking to ON is probably the best way to
go) It gives me just a tad more peace-of-mind,
and even more important, it matches my other switch. ;)
So, with the ability to have dual-speed trim, slow during cruise and
fast in the pattern, and the ability to prevent runaway trim issues, I
decided that I had finally stumbled on a product that I was willing to
mount into my plane. I had Bob send me one right away so I could
get it installed before my next trip.
Wiring the Safety-Trim
Those of you who know me know that I agonize over situations like
this. My existing trim system had now been working well since I
replaced the relay after OSH, and everything was going good. You
hate to buy a new product that makes certain claims and rip out a
working system for one that is unknown. I started by unmounting
my 2 relays, and letting them hang, and I sat and stared for a while,
wondering if I really wanted to do this. Finally, I just chopped
out the old relays. I wired the aileron circuit and power and
ground temporarily and gave it a quick test. Sure enough, it did
just what he said it would. 3 seconds of operation, dual speeds,
reversing, the whole thing. Well, time to start splicing and
re-wiring. I was initially going to make it all temporary and let
it hang and go for a flight, but every step of the way as I tested
things, it always worked fine, so I just kept working on making it
permanent. (Note, after the original writing of this article I added Rudder Trim and decided to
re-wire so that the rudder trim used the controller's 2nd axis, instead
of aileron trim. In the RV-10, Aileron trim could always be left
full speed and even if the trim ran away there is unlikely to be any
major handling problem. I did find that the rudder trim can
benefit from the 2nd axis being set to slow speed, however, so I
re-wired it as needed)
The thing I noticed right away is that this
thing was way easier to wire up than the standard
Aileron/Elevator Ray Allen relays that I had previously used.
Man, had I been able to install this system initially, it would have
saved me a lot of time as it's so easy to install, and I never would
have had that stuck relay problem in the first place. You can see
from the photos below, stolen from Bob's site, that it comes with a
complete (and well made, too, I might add) harness, ready to splice in
and install. I must say that I was a bit surprised at the
physical size of the box, being about 5 or 6" long, but it is much
lighter than it's size indicates, so I found a handy place just below
my radio stack where I could stick it in. You could wire it
anywhere, from the tail, the subpanel, or even under the seats.
It didn't take long and all the connections on the panel were done, and
I sat back amazed that it could be so easy to install. If I were
re-installing my Ray-Allen relays, it would take me a lot more time to
get it all in and done right.
** Installation note regarding switches: I called to verify on
this one, but as you know, the trim system works by pulling either of
the 2 input wires on the controller to ground, causing it to activate
in that direction. The standard Ray Allen switches can easily be
used by connecting the RED/WHITE wire of the switch to ground, which
pulls ONE of the 2 white wires to ground when activating, but when in
the neutral position, the 2 wires are basically tied together. This is
not a problem for the controller.
Regarding a retrofit...
One nice thing about this system is it's a very easy retrofit
installation. There is enough wire in the harnesses that if you
have all the relays mounted in the same general area, you should be
able to easily take a flying RV-10 and cut this system in without much
hassle. Other than the waste you go through buying relays as an
original installation, and then throwing them away later, there's no
reason why a person can't just fly it the "bad" way and do some
testing, and easily upgrade once they see how bad it really is.
It's a pretty drastic difference. I know how it is to sit
watching the email lists and wonder...."is it really worth it?" or "do
I really need that?", so perhaps what a person needs is to first
do their testing, and picture what they'd do in some situations where
the trim got wild. I think once a person discovers the "problem",
they'll want to take a preventative solution.
2-speed operation installation
I haven't mentioned this yet, but the RV-10 has one great method of
switching to that lower speed without relying on an airspeed
switch....a flap position switch. If you use the Van's flap
method of a flap position system, it gives you a -3 degree, a 0 degree,
and then 2 REAL flap settings of 15 and 25 degrees for use during
landing. The -3
setting is the reflex setting, typically only used in
cruise...precisely where you need the trim speed reduced.
Technically you
should be taking off with in either the Zero degree or the 15 degree
flap configuration, although I typically just leave them in reflex
unless I am on a short or turf runway. (When retracting from a
touch-and-go, they'll automatically go to reflex.) Not only that,
but you
can't activate the flaps to the lower settings until you are at lower
airspeeds. This means that if you put in a microswitch that will
sense when the flaps go into -3 reflex position, that would be a
perfect time to make your trim system run slower, as you use the reflex
position for cruise, yet during an instrument approach, dropping the
flaps to ZERO would be a preferred way to get set up for flying the
approach. Since you can't drop an additional notch of flaps until
you hit 87kts, you can bring them down to Zero and get your full-speed
trim function, and your position system is then just a click away from
dropping them to 15...you'll then be able to fly your approach at
100-120kts (90 or 100 inside the outer marker) and when you have the
runway in sight you can just drop the flaps and re-trim and have all
the trim speed you need. Beyond that, there are additonal reasons why
an airspeed switch is a good idea...keep reading on.
In thinking of how to install some sort of flap reflex switch, I had a
dilema. For one, it's a pain to access the tunnel. I didn't
want to have to re-adjust a microswitch and take apart the tunnel more
than one time. Then, how complex of a bracket would I need to
create. And, if I used a bellcrank, would it have too much travel
for a little limit switch....I don't want it to be mounted too far from
the torque tube, so that those 3 degrees of rotation don't add up to a
huge distance of arm travel to activate the switch. BINGO!
As I was replacing
my aux batteries, I came across the perfect location, and
eventually a perfect method.
Mounting a microswitch inside the place behind the
rear-seat-passenger's ankles that houses the flap torque tube (and in
my case the aux batteries), would be an easily accessible mounting
location. With the torque tube rotation, it rotates backwards as
the flaps come up. So I just needed to find a way to put an arm
on the torque tube, and have it swing into the microswitch.
Additionally, you need that arm to not start any higher than the 12
o'clock position because it will rotate into the cover panel. I
then realized that a hose clamp with a small piece of angle under it
(only about 1/2" wide) would be a perfect lever arm for the actuator,
and as I was digging through some scrap I found the perfect switch
mounting. From plans page 8-3, part HS-1008-L and -R, I had cut a
bit of a bad cut on one piece when I built the elevator, and being a
pack-rat I threw all old scraps into a box. One of those pieces
was just perfect for attaching to a microswitch (I used a VX-53-1C23
switch from mouser.com) and mounting to the floor panel next to the
torque tube. I glued it down with E6000 and screwed in 2
self-tappers to hold it down as well. As an overall arrangement,
it allows simple adjustment by loosening the hose clamp and adjusting
so at full-up travel the lever is pressing down on the switch all the
way. Then, when you deploy the flaps, about 1.5 degrees into the
rotation the switch clicks and you're now at full-speed trim.
(The 2-speed option just gets switched to ground when you want slow
speed) Simple, easy to get at, and absolutely perfectly effective!
So with it all installed, it's time to
fly!
Additional Note updated 2/29/09
Although the trim system has been working perfectly, with this being
the downtime of the year up here in the tundra, I have decided to play
with things a bit. Since Bob is now selling airspeed switches for
the speed selection, I got one and installed it in series with
the flap torque-tube switch that is already installed.
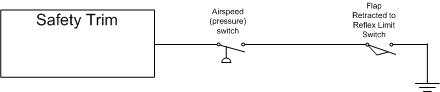
As you can see from how it now works, in order to have low speed
trim (for in cruise), you would have to have BOTH conditions
satisfied....the flaps fully retracted to reflex, AND airspeed above a
certain setpoint (default is 100kts). That way if you either slow
down below the
setpoint, or you drop your flaps to the zero flap point or further, you
immediately get full speed trim. Initially I didn't think this
was such a necessity, but let me explain why it may be more of a
concern than I thought.
I had been doing touch-n-go's with my wife a few weeks ago, and on
landing we were very nose-up on trim...toward the top of the 10 segment
LED. When you touch down and want to go-around, you don't want to
stay on the ground and run off the runway, so you need to start your
flap retraction and get that power back in for takeoff. Great,
except that the RV-10 has so much power that you'll be off the ground
in no time, yet if your flaps retract fully to -3, you'll suddenly be
set for low-speed trim, yet still in need of lots of trimming.
The flaps will retract much faster than the trim will travel from nose
up to takeoff configuration. I was finding that I'd be off the
ground with the flaps up, and not yet be trimmed all the way down to
comfortable climb. So, I installed the airspeed switch in series
as above, and now I will still always have high-speed trim all the way
until I am climbing out at 100kts or more. I was ititially
worried about cutting yet another item into my pitot system, but if you
use good tygon tubing and fittings, you won't have any leaks.
Trust me that with all it's power, speed, electric trims and flaps, and
all the gizmos that we have in our -10, it's important to make things
simple for those who are just starting to fly these planes. The
airplane can be a handful for a new pilot. I didn't see the need
for airspeed switching when all I was doing were cross-country flights,
but now practicing touch-n-go's I see a real benefit for the airspeed
switch.
Flying with
the Safety-Trim
Before my test flight, I was a bit worried about a couple things.
First of all, if you're time-limited to 3 seconds of trim, will that be
enough? Next, if it works by controlling the voltge to the motor,
will the motor stall with the controller set near it's lowest
setting? What about during takeoff? If I take off with the
flaps in reflex, will I get enough trim speed to handle a sudden change
in trim requirements at slow airspeeds? Well, let's get on with
the talk and answer some of those questions...
First, during takeoff, I intentionally trimmed it a bit out of trim
more than my normal takeoff position...a couple bars out on the
indicator. As it turns out, at the lower airspeeds you don't have
a ton of stick force to overpower, so flying the plane was just fine,
and the trim was plenty fast enough to correct some out-of-trim
ability,
even at near the lowest setting for slow-speed. No problem
there. The airspeed switch will help give you full speed trim for
all of the takeoff roll too. Also, 3 seconds was plenty of trim
for both my takeoff,
and all of the landing approaches. I didn't pay attention on one
landing and just flew as normal, and I was able to just use my normal
technique and noticed no negatives with a 3 second timeout. Then,
when I did fly one and watch what I was doing, I realized that when I
trim the plane, I'm holding stick force, I trim some force away, and
then I relase my pressure to test if it's "hand's off" or not. If
not, I trim some more. So, I probably rarely use a full 3 seconds
without testing it anyway, and even a couple microseconds of switch
release will re-set the timer.
As far as the motor stalling, nope, not a bit. The controller
doesn't allow you to set it so low that it will stall, and with the
trim being so sensitive in the -10 in cruise, it doesn't take a whole
lot of trim to make that tab move. So, we're good to go
there. I also tested the reverse function and it
worked as advertized. I'm
now not worried about inadvertent operation of the reversing because I
had to really consciously watch what I was doing to reverse my trim.
Now for the real safety testing...
I set the plane up at 135kts and the flaps at Zero. I held the
trim for 1 second and released. Within that one second I was now
rocketing towards the sky, and soon saw climb rates near 4000
fpm. I did the same thing starting at 135kts and the flaps in
reflex so I'd get slow trim and after 1 second I was climbing quick,
but nothing like I had with full-speed trim. You didn't get the
G-forces, the climb rate, and the slow airspeeds.
I decided to quantify it a bit more. I leveled out at 160kts
indicated, and tried again. This time with slow speed I held the
trim for 1 second and watched my G-meter. It had one brief and
instant blip of +1.4 G's as it started to climb. As I was
climbing, it was hard to approximate the climb rate because of the
constant change of rate as you lose power, but it looked like I was
climbing around 2000 fpm. Now time for the high-speed trim
test. With 1 second of trim activation, I was now pushing into
the 2+ G's of force, and my climb rate exceeded 3500fpm, and it was a
lot more extreme in how it pitched up. With slow-speed, you had
much more time to "feel" you were starting to climb, and react to it,
whereas with the high speed, it's a non-linear pitch feel...you don't
notice it much for the first little bit of time, but once it starts to
get out of hand, it really starts rocketing up.
Now for a more extreme test...
So this time I start at 160kts indicated, and at slow speed trim I hold
the switch for 5 seconds (it times out after 3), and give it a chance
to do what it would if I had runaway trim. The airplane climbs
fast, but I never see more than a quick blip of the G-meter showing
up...it declutters at < +1.4, so you only see it when you hit +1.4
G's. I let it continue the climb and it climbs higher until it
gets into the 90's IAS, but then the nose naturally starts to drop,
seeking it's new trim speed, and it seems to settle out at about
125kts. So 3 seconds of trim takes you to 125kts of trim from
160. I start the same test with 160kts and high-speed trim, but I
cannot let myself allow it to go for 3 seconds. The plane becomes
too uncontrollable if you let it get near 3 seconds. The G-forces
are well into the 2's on the pitch up, and I'm sure that the speed it
trimmed to would be somewhere near either very slow flight or stall,
and I didn't want to take the time today to test and see if it would
actually pull up into a stall with 3 seconds of NORMAL RV-10 trim.
So there you have it, a real-life proof that this system can add to
safety in the RV-10. For one thing, after testing it, I am
convinced that if someone did indeed have a full runaway trim with
elevator in an RV-10, it would be a disaster. You'd never get to a
breaker or disconnect switch in time. If it were a pitch down,
you'd not only likely overstress the negative G capability of the
airframe, but you'd be flying light in your seat and smacking your head
on the cabin top. Limiting the trim to 3 seconds would help, but
if you get 3 seconds of high-speed trim, I am not convinced that in
every case a pilot would have the quick reaction to be able to recover
before they get tossed about the cabin. Now, slow it down while
in cruise, and then add on the 3 second timeout, and you have a system
that can run to it's 3 second limit and still not leave the plane
uncontrollable, and not push it into a stall. It's perfect for
cruise operation, and lets you more precisely trim the plane.
Drop the flaps just 3 degrees to the zero position, and you have your
normal trim system back, with the exception of the fact that you still
have the protection of a 3 second timeout. And to top it off, the
3 second timeout doesn't affect your ability to trim the airplane in
the pattern, so you're able to perform all of your piloting in a safe
manner. (Note that Bob did tell me that he has a way to
factory-adjust that timeout so if you for some reason decide you need 4
seconds or something like that, he can make that work for you)
Negatives? Well, since I don't yet have rudder trim installed
(hopefully VERY soon), I have my ailerons tied in to the system, and
although I like having the trim runaway prevention, I don't need slow
speed on my ailerons. So I may re-wire when I install rudder trim
and run the rudder through the controller instead.
(Note, after the original writing of this article I added Rudder
Trim and decided to re-wire so that the rudder trim used the
controller's 2nd axis, instead of aileron trim. In the RV-10,
Aileron
trim could always be left full speed and even if the trim ran away
there is unlikely to be any major handling problem. I did find
that
the rudder trim can benefit from the 2nd axis being set to slow speed,
however, so I re-wired it as needed)
After flying with this system in my plane, I'm convinced that this is a
real safety feature for the RV-10. Personally, I think it's
something that should be made standard on this 4-place family x/c
plane. After a few of us having relays fail in short order, and
after at least a few of us personally seeing the effects of inadvertent
trim activation during cruise, I really see this as a major safety
improvement for our planes. You'll spend more than buying 2
relays and 2 speed controls from Ray Allen, but you're not just
replacing those parts for a nice solid-state controller, you're adding
runaway trim prevention, reversing capability, tons of safety, and a
lot easier wiring installation.
See below for photos of my install. Note the panel switch located
near my quadrant for quick but protected (by that large knob)
operation. Then see the photos for how the flap sensing switch is
mounted. I think that will be a very easy way for people to add
such a sensor to their system without going out to the wing roots or
into that tunnel.
Here are a couple pages of the info sheet that I grabbed from their
site. It shows the wiring arrangement, and a spec sheet for the
system.
|
|