RV-10 Wheel Fairing Mount Repair
Finished 11/7/2010 - 686 hours
approx.
Updated 11/23/2010
Somewhere in the last 100 or so hours, I've been noticing that my wheel
fairings can be rocked up and down between the nose and the tail,
rotationally around the axis. You notice it when you are wiping
them down and cleaning off the bugs. The fairing kind of clicks
up and down, and you feel the looseness and slop in the way that the
fairing mounts to the gear leg. If you remember from building the
gear legs, brake mounts, and fairing mounts, you mount a cleveland
brake mount to the gear leg, and then from that you have some aluminum
spacers p/n U-1008 that you fabricate from some aluminum tubing, to a
length of 21/32" (.656"). These are 1/4" I.D. and 3/8"
O.D. The issue is, with the weight of the entire fairing being
held by these 3 spacers stuffed up against the fairing mount U-1010-L
(and -R), and also held by the stainless screw on the axle extension,
there's a lot of weight rocking around on 3 spacers that have a very
short arm from the pivot point. This means that all that rocking
will eventually wear those spacers into the aluminum part that holds
the fairing...causing damage.
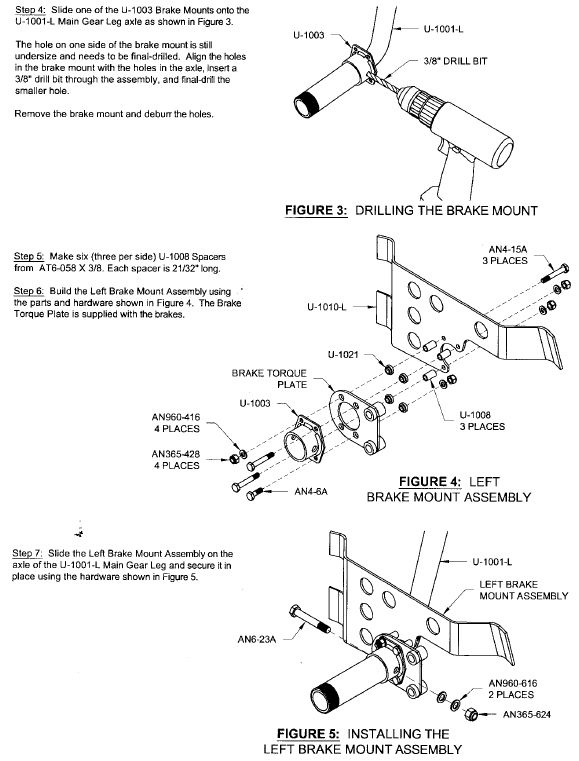
This issue is one that will probably eventually bite every RV-10
builder who doesn't fix the issue before it starts. After doing
this work, I believe that this is something that should perhaps be
improved in the original construction, and there may be an opportunity
for an aftermarket RV-10 part maker to help with a better fix.
I first became aware of the problem a couple years ago when another
RV-10 builder, I believe Bill D., found this problem on his
plane. At the time, I had quite a few hours and hadn't been
having any real big issues, so I took a "wait and see" approach to it,
and finally it got to be a problem more recently, so it was time to
act. Luckily there wasn't any significant damage to ruin any
parts, so a fix isn't too complicated. I think if you build it
well and keep the parts tight, you can probably
minimize the damage for a while. Mine certainly weren't serverely
damaged, but the first time I heard of this problem I think maybe Bill
had a little more damage than this...not sure. Either way, if you
only have the stock setup, make sure you keep those nuts torqued every
annual until you do a permanent fix, so that you don't get excessive
wear.
Here is a short video in .mov format where you can see the rocking of
the mount as I wiggle it.
Here are some pictures of the area, taken before I started fixing
it. In the 4th picture below you can see the slight wearing of
the aluminum plate where the spacers were digging in.
To fix the problem, you have to basically take all the parts off the
axle, including removing the U-1003 holding bolt so you can slide it
down the axle enough to remove the bolts holding the fairing mount
U-1010-L, as some of the bolts won't come out due to clearance issues,
without moving U-1003.
To fix the issue, the ideal fix would be to make new spacers out of
1/2" O.D. x 1/4" I.D. hardened steel (maybe stainless would be great if
you could find them). The reason is, the top-hat shaped bushings
U-1021 that go into the brake torque plate, are 1/2" I.D., and the
bolts holding this assembly are 1/4" bolts. I didn't have
good access (especially on the weekend), to custom parts, or even good
hardened parts, but I did have a Fleet Farm (Farm store) near by that
had all sorts of hardware individually packaged. I found a couple
of options and bought them both, for less than a buck a pack.
My first option was that they sold some steel spacers zinc plated that
were the same size as my aluminum spacers and 3/4" long...these could
be trimmed and would be probably better than the alumimum spacers that
were on there. My aluminum spacers had started to mushroom out on
the ends from torquing them down.
My second option was that they also sold steel spacers that were 3/8"
I.D. and 1/2" O.D. that would slide in a pressed-fit manner, right over
top of my existing aluminum spacers. This was the option I used,
and it has a side benefit...the bolt is steel and the inside of the
spacer is aluminum, so it's unlikely that they'll rust together some
day. If the spacers were steel, I'd probably lubricate them with
grease before assembly to make sure that they're removable in the
future.
As you can see in the photos below, the 1st photo shows the big steel
spacer and how it fits over the aluminum spacer.
The 2nd photo shows the variety of parts I could choose from. The
big spacer came in 2 lengths, one long enough that I could cut 2 from
one piece, since I needed less than .652" of length, and these were
1.5".
The 3rd photo shows the plain small steel spacer that I could just trim
to fit if I wanted.
After I went the route of cutting a large spacer to fit over the
standard aluminum one, the bottom 2 photos (#5 and #6) show the
resulting parts that I re-installed. The steel outer shell will
keep the aluminum from being able to mushroom out, too.
Now, to keep this from being a long-term chronic problem that damages
my U-1010-L, I added some steel washers to the inside, and shortened
the length of the original spacers to .600" to accomodate the added
thickness caused by the large washers. I bonded the washers to
the part using JB Weld after slightly scuffing the aluminum part, and
bolted it all up to let it cure. Worried about interference from
the fit of the entire round washer, I pinched the washers in place with
temporary bolts and trimmed around the original curves with an angle
grinder until the curves were very close, and then I used a scotchbrite
wheel to match them up and make everything smooth around the outside of
the U-1010-L.
As you can see in the first photo below, everything is bolted up to
cure, and the spacers now have more surface area, and a good steel wear
surface to protect the U-1010-L. The part on the other end is
already hardened steel and won't be a problem.
After doing this job, the wheel fairing is now perfectly solid and
shouldn't be a problem again...maybe it won't even need re-torquing.
A side note: It may be a good idea to swap out the nyloc nuts for
good all-steel high temp locknuts. I didn't see any problems with
mine, but if you have a brake issue, you may generate a lot of heat,
and it may be enough to melt the nylon. Again though, I saw no
evidence of this on mine.
The only real sad part about this problem is that just like the poor
design of the original axle extensions, and the original front axle
spacers, this is another part on the RV-10 that will turn into a
chronic problem for many RV-10 builders...and sadly, there are so many
of them that won't read this that it's going to affect a lot of
people. It would be nice if some different steel tubing or steel
spacers were supplied with the kit along with instructions on the use
of washers or something to prevent wear, but I'm guessing this will
never happen. On the upside, the Axle extensions were fixed by a
huge number of people, with 3rd party parts being available to fix the
issue, and the Matco axle does a great job of taking care of the
nosewheel problem. Maybe we'll get an RV-10 parts maker that will
come out with some custom machined steel washer parts and steel
spacers, so that new builders can just buy those parts and have the
improvements from day 1.
11/23/2010 Update
There are now places for a builder to actually BUY the parts to fix
this problem. First to market was PlaneAround.com with the spacers
pictured below. These are a one-piece aluminum spacer that
provides a lot more surface area against the aluminum bracket. It
fits right in and should provide a good long-lasting fix. PlaneAround.com is the producer
of probably the most successful door latch replacement available for
the RV-10.
There is also work underway by PlaneInnovations.com which
should be producing something soon as well. They produce a
variety of parts including the axle extensions very similar to the ones
I had helped get made many years ago.
Here are photos of the spacers by
PlaneAround.com
Site Home
|
N104CD Home